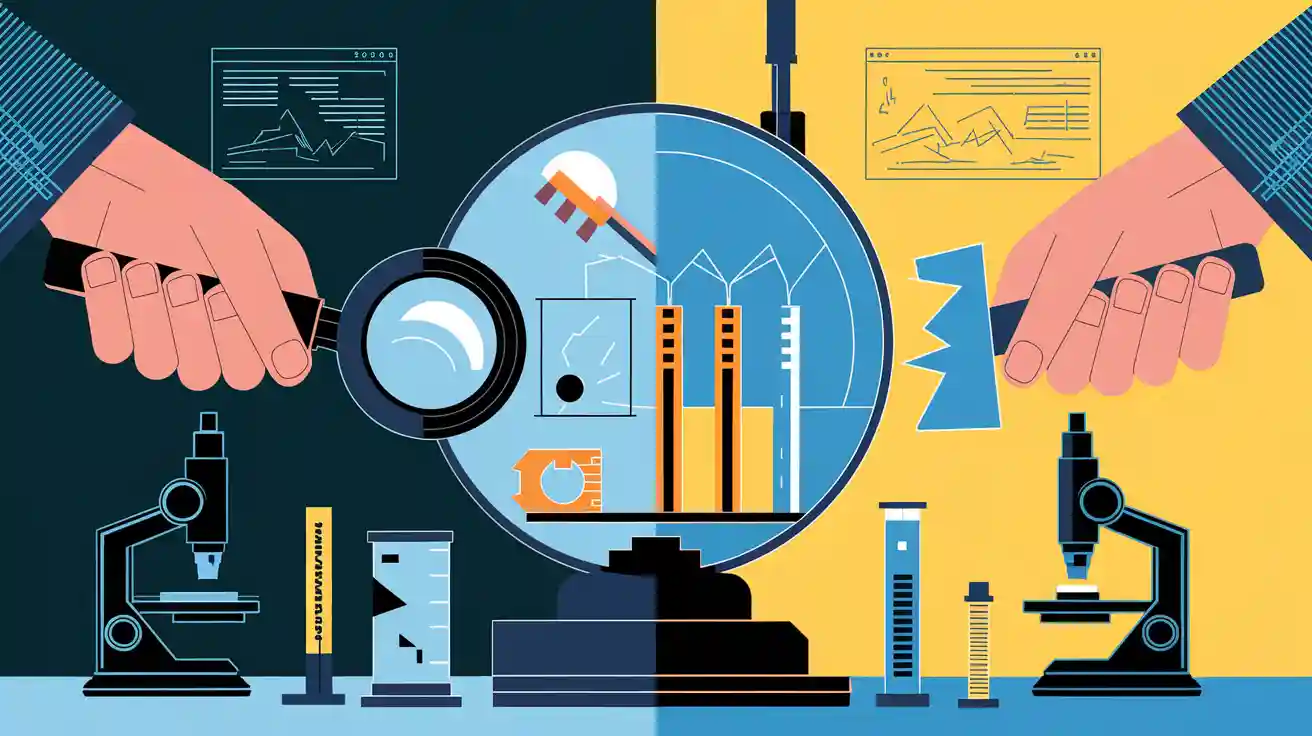
When testing metals, you can choose between destructive testing and non-destructive metal analysis. Destructive testing breaks or bends the material to assess its strength, while non-destructive metal analysis examines the material without causing any harm, keeping it intact.
Selecting the appropriate test is crucial for obtaining reliable results and preserving the material. Chẳng hạn:
Studies on recycling metals from waste indicate that testing must be precise. Tools like the Augmented Dickey–Fuller test assist in identifying unusual data.
The field of metal testing is expanding rapidly. The market is projected to grow from $28.63 tỷ trong 2025 đến $52.38 tỷ bởi 2034.
These trends highlight the importance of robust testing methods for industries such as aviation and automotive. Safety and performance are paramount. Understanding when to utilize destructive testing versus non-destructive metal analysis enables you to make informed decisions.
Bài học chính
Destructive testing breaks materials to check strength but ruins them.
Non-destructive testing finds flaws without damage, good for expensive items.
Picking the right test depends on material, quy tắc, and cost limits.
Destructive testing helps study failures, while non-destructive testing ensures safety.
Both tests are useful; knowing their differences aids smart metal testing.
Destructive Testing Methods
Common Techniques in Destructive Testing
Destructive testing uses methods to check how strong and durable metals are. These tests often break or change the material to learn about its properties. Some popular techniques include:
Tensile Testing: This test pulls a metal piece until it snaps. It shows how much force the metal can handle and how far it stretches.
Impact Testing: A hammer or pendulum hits the metal to see how tough it is and how well it handles sudden hits.
Hardness Testing: A hard tool presses into the metal to measure how resistant it is to dents or scratches.
Fatigue Testing: The metal is stressed over and over to find out how long it lasts before breaking.
Metallurgical Analysis: The metal is cut, đánh bóng, and treated to study its tiny structures. This helps find problems like cracks or rust.
These tests are important for industries like building, xe hơi, và các nhà máy. They make sure materials are safe and work well. Chẳng hạn, cutting a metal part in half during testing shows hidden flaws inside. Experts check these tests to make sure the results are correct.
Evidence | Sự miêu tả |
---|---|
Destructive tests | Cutting metal parts in half reveals hidden flaws inside. |
Certified inspectors | Experts ensure testing is done properly for accurate results. |
Mechanical testing | Shows how materials behave under certain conditions to meet standards. |
Advantages of Destructive Testing
Destructive testing has many benefits that make it useful for studying metals. These include:
Chính xác: Changing the material gives exact details about its strength and hardness.
Độ tin cậy: Careful testing by experts ensures the results are trustworthy.
Failure Analysis: This test helps find out why metals fail, like cracking or rusting. Chẳng hạn, studying the metal’s structure shows weak spots.
Industry Applications: Destructive testing is key for industries like cars and buildings. It checks if materials can handle wear, scratches, and stress.
Real-life examples show how helpful destructive testing is. One case found the cause of a factory fire due to a broken bolt, helping prevent future fires. Another example showed how a car company improved testing tools to get better results.
Limitations of Destructive Testing
Destructive testing works well but has some downsides you should know:
Material Loss: This test damages the sample, so it’s not good if you need to keep the material.
Limited Scope: It only tests small pieces, which might not represent the whole batch.
Chi phí: It can be pricey because of special tools and wasted materials.
Human Factors: Results can change based on the inspector’s skills and decisions.
Even with these issues, destructive testing is still a trusted way to check quality. It gives useful information to keep metal parts safe and reliable.
Testing only small amounts and human errors show the need for other methods too.
But its ability to find problems and stop future failures is very important.
Applications of Destructive Testing
Destructive testing helps keep materials safe and reliable in many industries. By pushing metals to their limits, weaknesses can be found. It also shows how materials perform under tough conditions. Here are some ways destructive testing is used:
Corrosion Testing: This checks how metals handle rust in different places. It’s important for materials used in oceans or chemical factories.
Fracture and Mechanical Testing: Cracks and flaws are tested to see how they affect strength. This is crucial for buildings and bridges.
Aggressive Environmental Testing: This tests how materials work in extreme heat or pressure. It’s often used for oil and gas pipelines.
Fatigue Testing: Repeated stress is applied to see how long materials last. This is key for airplane wings and car parts.
Residual Stress Measurement: This checks if materials can handle heavy loads over time. It’s used in industries like aerospace and cars where safety matters most.
Tensile Testing: Controlled force is applied until the material breaks. This ensures metals are strong enough for building and manufacturing.
Mẹo: Destructive testing isn’t just about breaking things. It gives data that saves lives and prevents accidents.
Industries like cars, planes, and buildings depend on destructive testing. Earthquake tests check if building materials can survive shaking. Car crash tests show how strong frames and safety gear are. Airplane makers use these tests to ensure parts are safe for passengers.
These methods help understand how materials behave. They also guide decisions about where materials can be used. Though samples are destroyed, the knowledge gained is worth the cost.
Non-Destructive Testing Methods
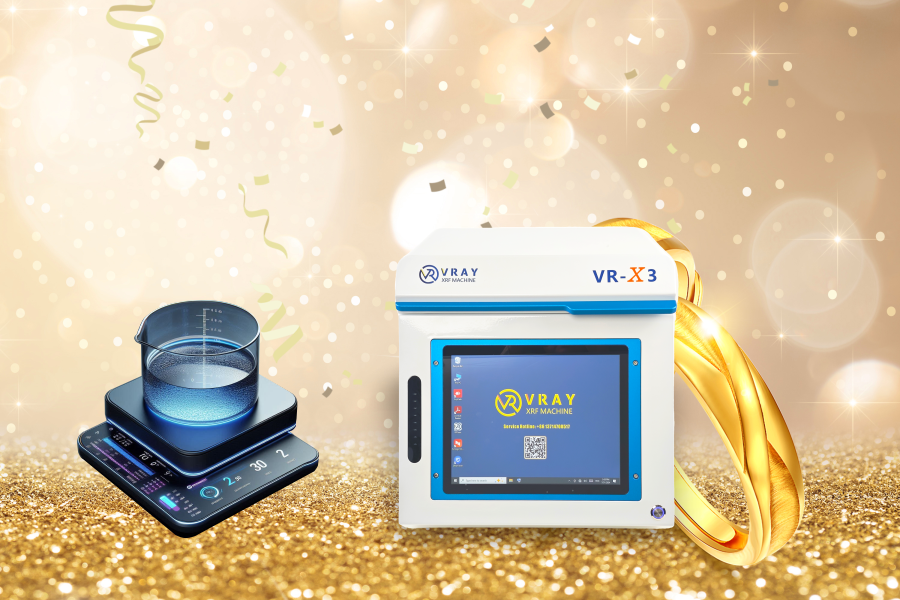
Non-destructive testing (NDT) checks metals without breaking them. This method keeps materials whole while giving useful details about their condition. Industries like airplanes, buildings, and factories use NDT to stay safe and work well.
Common Techniques in Non-Destructive Testing
NDT uses different ways to check materials. Each method has a special job and gives accurate results. Here are some common ones:
Ultrasonic Testing (UT): Sound waves go through the metal to find cracks or holes inside.
Magnetic Particle Inspection (MPI): A magnetic field shows surface and near-surface defects using iron particles.
Liquid Penetrant Testing (LPT): A colored liquid fills cracks. A developer makes flaws easy to see.
Radiographic Testing (RT): X-rays or gamma rays take pictures of the inside to find hidden problems.
Visual Testing (VT): Inspectors look for surface issues using their eyes or tools like magnifiers.
Ghi chú: Automated NDT Phương pháp, like short-wave radiation, work very well. Chẳng hạn, data tools help find flaws in tricky items like welded joints.
Advantages of Non-Destructive Testing
NDT has many good points that make it very useful:
Material Stays Intact: Unlike breaking tests, NDT keeps materials undamaged. This is great for costly parts.
Tiết kiệm tiền: No material loss means less waste and lower costs.
Works on Many Materials: It can test metals, concrete, và hơn thế nữa.
Finds Problems Early: NDT spots issues before they get worse, keeping things safe.
Can Be Automated: Machines can do NDT, making it faster and reducing mistakes.
A study shows more industries now use NDT. Chẳng hạn, builders use it to check concrete for cracks. This shows how important non-damaging tests are becoming.
Limitations of Non-Destructive Testing
Even though NDT is helpful, it has some downsides:
Needs Skilled Operators: Some methods, like visual tests, depend on the inspector’s skill.
Expensive Tools: Advanced methods, like X-rays, need costly machines.
Material Limits: Some tests, like magnetic ones, only work on certain metals.
Calibration Needed: Nhiều NDT methods need standards to work correctly, which can be tricky.
Phương pháp | Lợi thế | Khó khăn |
---|---|---|
Liquid Penetrant Testing | Cheap, easy to carry, simple to use | Only finds surface flaws, needs cleaning |
Magnetic Particle Inspection | Good for subsurface flaws, cầm tay | Only works on magnetic metals |
Infrared Thermography | Can check from far away, shows heat images | Costly, needs standards for accuracy |
Visual Testing | Quick, can use machines, good for surface flaws | Depends on operator, misses hidden problems |
Even with these issues, NDT is key for quality checks. It ensures safety and reliability without harming materials, making it a must-have tool.
Applications of Non-Destructive Testing
Non-destructive testing (NDT) helps keep materials safe and reliable. It checks for problems without breaking or damaging the material. This makes it very useful in industries where keeping materials intact is important.
Real-World Uses in Industries
NDT is used in many fields like oil, gas, airplanes, and buildings. Each method has a special job to find flaws and ensure safety. Here’s a table showing how NDT methods are used in real life:
NDT Method | How It’s Used |
---|---|
Ultrasonic Testing (UT) | Checks welds in pipelines and tanks to ensure they are strong and free of defects. |
Radiographic Testing (RT) | Looks inside pipes for blockages, thinning, or buildup to keep them working well. |
Magnetic Particle Testing (MT) | Finds cracks on the surface or just below it in magnetic materials like welds and drill pipes. |
Penetrant Testing (PT) | Spots surface cracks in solid materials, often used on oil platform parts and welds. |
Why Use NDT?
NDT finds problems early, saving money and avoiding accidents. Chẳng hạn, ultrasonic testing keeps pipelines strong by finding weak welds. Radiographic testing spots blockages in pipes, keeping them efficient. Magnetic particle testing checks drill pipes for cracks, ensuring safety. Penetrant testing finds surface flaws on oil platform parts, preventing failures.
Mẹo: Adding NDT to your safety checks can save costs and improve safety.
Industry-Specific Examples
In airplanes, NDT checks if wings and parts are safe to use. In construction, it tests the strength of concrete and steel. Factories use it to inspect machine parts for safety. Oil and gas companies rely on NDT to check pipelines and tanks, avoiding spills.
Using NDT helps industries stay safe, reduce waste, and work better. These methods are crucial for places where safety and accuracy are a must.
Comparing Destructive and Non-Destructive Testing
Cost Considerations
Non-destructive testing (NDT) usually costs less than destructive testing. NDT checks materials without breaking them, saving money on repairs. Chẳng hạn, industries using NDT can find problems early. This prevents shutdowns and expensive failures. Fixing issues ahead of time lowers maintenance costs and keeps things running smoothly.
Destructive testing damages the sample, which raises costs. You might need to replace tested parts, especially if they are expensive. A report shows NDT reduces material waste and keeps operations running. This makes NDT a smart choice for saving money.
Testing Method | Cost Implications | Benefits |
---|---|---|
Thử nghiệm không phá hủy | Saves money, keeps materials intact, avoids shutdowns | Prevents failures, lowers repair costs, improves efficiency |
Thử nghiệm phá hủy | Costs more due to damaged samples and replacements | N/A |
Time Efficiency
NDT methods save time by working quickly without stopping production. Techniques like ultrasonic testing inspect materials fast and keep operations going. This is helpful for industries where delays cost money. Automated NDT tools can check big items like pipelines or airplane parts in less time than destructive tests.
Destructive testing takes longer because it damages samples. Preparing materials, kiểm tra, and reviewing results can be slow. Production might stop to get test samples, causing delays. Choosing NDT saves time and keeps materials safe.
Accuracy and Reliability
Both methods give reliable results, but their accuracy depends on the job. Destructive testing changes the sample to measure strength or hardness. This makes it very accurate for finding problems and checking quality.
NDT finds flaws without harming the material. Tools like ultrasonic testing spot hidden defects with great accuracy. Studies show advanced NDT tools, like the CAPO Test, are more reliable than basic ones like the Rebound Hammer. Software like STATUS 5 uses data models to improve NDT Chính xác.
Testing Method | Sample Size | Compressive Strength Correlation | Statistical Significance |
---|---|---|---|
Rebound Hammer | Basic models | Less reliable | |
CAPO Test | 80 tests | Mô hình nâng cao | More reliable |
Using modern NDT tools gives accurate results while keeping materials intact. This makes NDT a great choice for many industries.
Material Integrity and Preservation
Keeping metals strong and undamaged is often very important. Lựa chọn giữa destructive testing (DT) và non-destructive testing (NDT) affects whether the material stays usable after testing.
DT changes or damages the tested material. Tests like tensile or impact testing stretch, break, or bend the metal to check its strength. This gives accurate results but ruins the sample. Chẳng hạn, a metal beam tested for tensile strength cannot be reused because it gets permanently bent or broken.
NDT, Tuy nhiên, keeps the material whole. Methods like ultrasonic or radiographic testing find flaws without harming the object. This lets the tested item stay in use or be reused later. Industries like airplanes and buildings often prefer NDT because keeping materials intact is very important.
Here’s a table showing how these tests affect materials:
Testing Method | Material Impact | Usability |
---|---|---|
Thử nghiệm phá hủy (DT) | Damages or changes the material | Cannot reuse the tested sample |
Thử nghiệm không phá hủy (NDT) | Keeps the material intact | Allows reuse or continued service |
The choice depends on your needs. If you need detailed strength data, DT might be required even though the sample is lost. But if keeping the material undamaged matters most, NDT is the better option.
Mẹo: Sử dụng NDT when reusing materials is important. It saves resources and reduces waste.
Choosing the Right Testing Method
Factors to Think About for Metal Analysis
Picking a testing method for metals depends on many things. The material type and its features are very important. Chẳng hạn, magnetic metals work best with magnetic particle inspection. Ultrasonic testing is good for finding inside flaws in non-magnetic metals. Following rules like ASTM D638 for tensile testing ensures your results are correct and useful.
Some tools can help you decide. High-speed workflows collect data faster than old methods. They save time but might have small errors or changes in results. Here’s a table comparing workflow types:
Workflow Type | Time Saved | Errors | Result Changes |
---|---|---|---|
Ground-Truth | 1x | Không có | Không có |
Previous Study | Không có | Không có | |
High-Speed Workflow | 5x | Some | Some |
Knowing these details helps you pick the best testing method for your needs.
Testing Methods for Different Industries
Industries use special tests to meet their needs. Builders, car makers, and airplane companies follow ASTM rules to check materials. ISO rules are used worldwide to ensure safety and quality. Some industries make their own rules, like testing airplane parts for strength and wear.
Standard Type | What It Does | Used By |
---|---|---|
Rules for testing metals’ quality and compatibility. | Builders, Car Makers, Airplane Companies | |
ISO Standards | Global rules for safety and quality. | Many industries worldwide |
Custom Industry Standards | Special rules for unique needs, like airplane part testing. | Airplane Companies |
Using these rules makes sure your tests meet industry needs.
Finding the Right Balance: Chính xác, Chi phí, and Saving Materials
Choosing between destructive and non-destructive tests means balancing accuracy, cost, and saving materials. Non-destructive tests, like ultrasonic testing, don’t damage materials. They save money and reduce waste, making them good for long-term use. Advanced methods also help follow environmental rules.
Data shows why this balance matters. Good testing plans improve success rates and lower costs. Chẳng hạn, the Debug option is cheap and quick, taking only two minutes to learn. The Heavy option is more accurate but costs a lot more.
Mẹo: Think about your material type, quy tắc, and budget to choose the best testing method.
Knowing the difference between destructive and non-destructive testing is important. Destructive testing changes the material to give exact results. Non-destructive testing keeps the material whole so it can be reused. Each method is useful for different goals.
The right choice depends on your industry and needs. Advanced tools like ICP-MS/ES are popular because they are very sensitive. They can check many elements at the same time. This shows that people prefer fast and accurate testing that follows strict rules.
Think about what you need before deciding. Look at costs, saving materials, and meeting industry rules to pick the best testing method for your job.
FAQ
What is the main difference between destructive and non-destructive testing?
Destructive testing breaks the material to study its strength. Non-destructive testing checks materials without harming them. Use destructive testing for detailed strength checks. Use non-destructive testing to keep materials safe during inspections.
Which industries benefit most from non-destructive testing?
Industries like airplanes, buildings, and oil pipelines use non-destructive testing. It helps check airplane wings, pipes, and structures without damage. These industries rely on it to ensure safety and quality.
Can non-destructive testing replace destructive testing?
Non-destructive testing cannot fully replace destructive testing. Both have different uses. Destructive testing is best for finding why materials fail. Non-destructive testing works well for regular checks or saving materials.
How do you choose the right testing method?
Think about the material, quy tắc, and your goals. Destructive testing is good for strength checks. Non-destructive testing is better for finding flaws in reusable materials.
Are non-destructive testing methods expensive?
Some non-destructive tests, like X-rays, need costly tools. But they save money by reducing waste and avoiding failures. Cheaper options like visual or liquid tests work for simple checks.
Mẹo: Match your budget and needs to pick the best method.
WhatsApp
Quét mã QR để bắt đầu trò chuyện WhatsApp với chúng tôi.