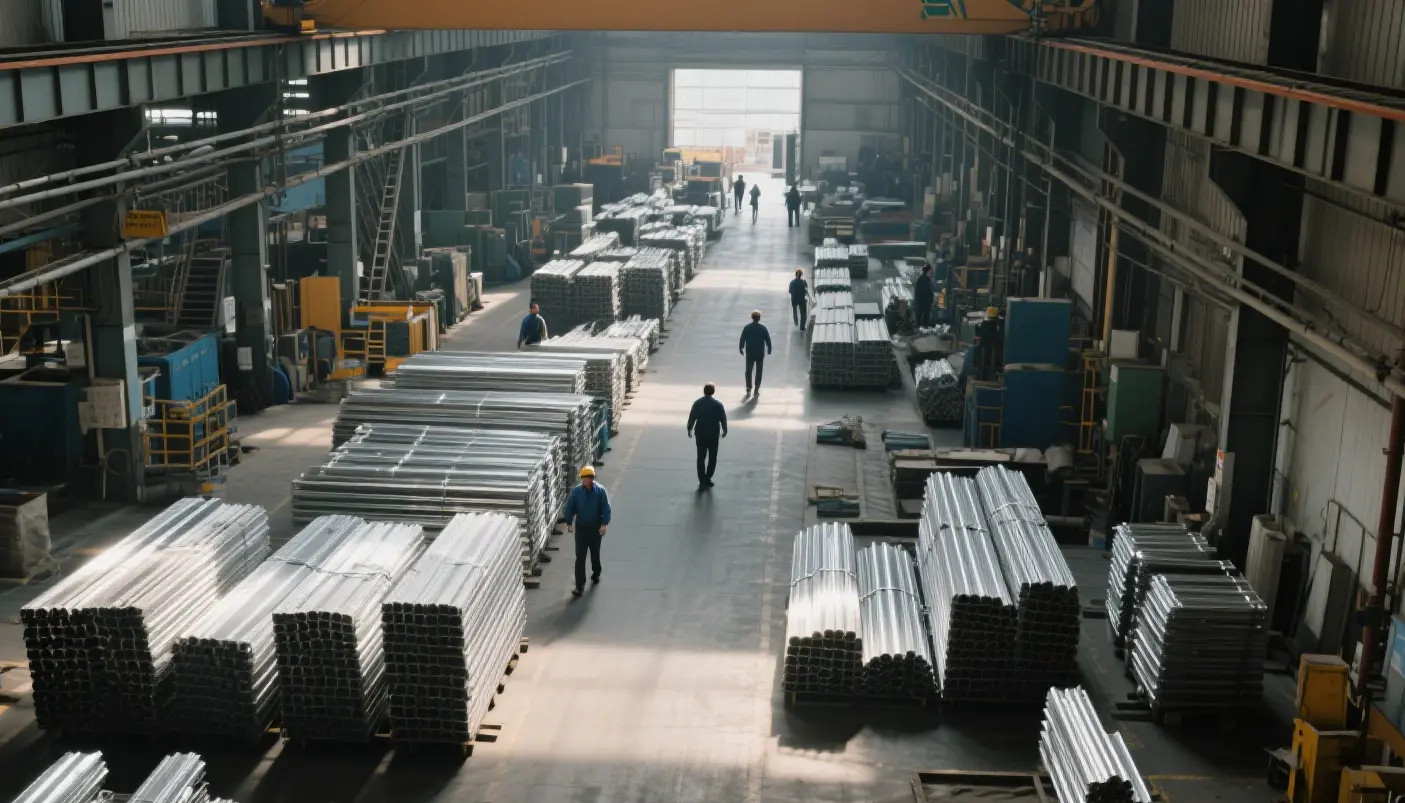
You can use modern stainless steel analysis methods like XRF, OES, AAS, ICP-OES, XPS, magnet, visual, and chemical spot tests. These tests help you check stainless steel fast and correctly. They help you check for quality, safety, and if the alloy is real. People test stainless steel to make sure it follows rules and works well. Some stainless steel analysis methods like potentiodynamic polarization give you numbers for corrosion resistance. Using the right tests can make tools last up to 300% longer. Always pick the best test for what you need.
Key Takeaways
Use modern stainless steel tests like XRF, OES, and chemical spot tests to find out steel grades fast and correctly. These tests help make sure the steel is good quality.
Get samples ready by cleaning and polishing them well. This helps you get good test results and stops mistakes from happening.
Handheld tools like XRF analyzers let you test steel quickly in the field. You can use them without hurting the metal.
Compare your test results to standards and charts. This helps you know the steel grade and check if it is safe and resists rust.
Always follow safety rules when testing. Use more than one method to check your results for the best accuracy and to help your project succeed.
Stainless Steel Analysis Methods
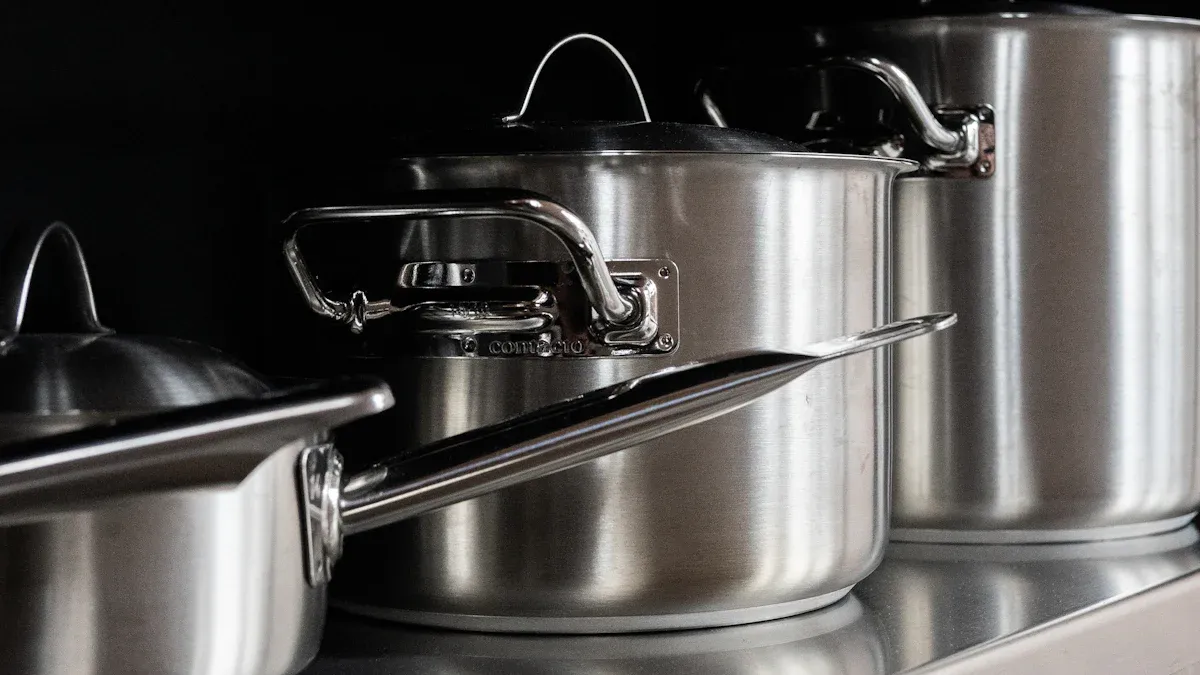
Modern stainless steel analysis uses many ways to test. Each way helps you find grades fast and correctly. Some tests work best outside the lab. Others need special lab tools. Pick the right test for your needs. Think about how fast, how exact, and what tools you have.
XRF Analyzers
XRF analyzers use X-ray fluorescence to check elements in stainless steel. You can use handheld tools for quick, safe testing. These tools give results in seconds. They work well in factories and scrap yards.
Modern XRF analyzers, like the ESI H-500, are very exact. For stainless steel 316, the chromium result is close, about 0.2% off. For manganese, it is about 2.7% off. These tools can find elements from 1 तिर 500 ppm. For stainless steel 304, accuracy for chromium, manganese, nickel, copper, and molybdenum is between 94.5% and 99.5%. You can trust these tools for good stainless steel analysis. XRF works best for grades with lots of chromium and nickel, like 304 and 316. XRF does not work well for light elements like carbon.
Tip: Use XRF analyzers when you need fast, exact, and safe results outside the lab.
OES and ICP-OES
OES and ICP-OES are lab tests. You use these when you need very exact results. OES uses a spark to excite atoms in metal. ICP-OES uses plasma to do this.
ICP-OES finds tiny amounts of elements.
It gives very exact and correct numbers.
This test follows strict rules and can find over 30 elements.
ICP-OES works well for hard samples and has a big range.
Using ICP-OES in quality checks can cut equipment failures by over 70%.
ICP-OES meets the Chinese rule GB/T 20125-2006 for stainless steel analysis. Use OES or ICP-OES to check for tiny impurities or when you need certified results. These tests help you find grades like 304, 316, 321, and duplex stainless steels.
AAS and XPS
AAS and XPS are advanced lab tests. You use AAS to measure certain elements, like nickel or chromium, with high exactness. AAS is good for checking small amounts of elements in stainless steel.
XPS helps you study the surface of stainless steel. You can use XPS to look at thin coatings or surface treatments. This test gives you details about the chemical state of elements on the surface. Use XPS when you need to know about surface makeup or dirt.
Both AAS and XPS need special tools and trained workers. You use these tests for research, quality checks, or when you need deep stainless steel analysis.
Magnet and Visual Tests
You can use a magnet to quickly check stainless steel grades. Austenitic grades, like 304 and 316, are not magnetic. Ferritic and martensitic grades, like 430 and 410, are magnetic. Duplex grades are a little magnetic.
Stainless Steel Grade Family | Magnetic Response Level | Relative Permeability Range | Example Grades |
---|---|---|---|
Austenitic | Non-magnetic | 1.003 – 1.005 | 304, 316, 321 |
Ferritic | Strongly magnetic | 500 – 1000 | 430, 409, 439 |
Martensitic | Strongly magnetic | N/A | 410, 420 |
Duplex | Moderately magnetic | 20 – 100 | 2205, 2304 |
You can also look at the surface to check finish and shine. Trained inspectors can tell apart main stainless steel grade families up to 80% of the time. The magnet and visual tests help you with quick first checks. Always check results with other stainless steel analysis methods.
Chemical Spot and Spark Tests
You can use the acid test, chemical spot test, and spark test for fast, cheap checks. The acid test uses special chemicals to react with elements like molybdenum or nickel. The chemical spot test can be up to 95% correct, especially for telling 304 from 316. The acid test is easy and good for quick checks.
The spark test uses a grinder to make sparks from the metal. You look at the color and shape of the sparks to tell the grade. The spark test can be up to 75% correct. You need training to read the sparks right.
Test Method | Success Rate / Improvement | Key Details and Validation Points |
---|---|---|
Spark Testing | Up to 75% accuracy | Based on over 1,000 samples; good for telling main stainless steel grade families; needs trained people. |
Chemical Spot Testing | Special molybdenum detection helps tell grades like 304 and 316; fast first check. | |
Protocol Enhancements | Up to 60% less time to check | Standard steps like surface prep, temperature control, checked chemicals, and digital notes make tests better and faster. |
Use the acid test, chemical spot test, and spark test for quick sorting or when you do not have fancy tools. Always check your results with other stainless steel analysis methods for important jobs.
How to Test Stainless Steel
Preparation Steps
Before you test stainless steel, you need to prepare your sample. Good preparation helps you get the right results. Follow these steps:
Clean the metal surface with a soft cloth to remove dirt and oil.
Use fine grinding paper to smooth the area you want to test. Avoid coarse grinding, which can change the metal.
Polish the surface with a diamond paste or a special cloth. This step removes scratches and makes the surface shiny.
For some tests, use a chemical etchant. Pick the right etchant for your stainless steel type.
Dry the sample before you start testing.
Tip: Careful preparation helps you avoid mistakes when you test stainless steel.
Using Handheld Devices
Handheld devices make it easy to test stainless steel in the field. You can use tools like XRF or LIBS analyzers. These devices are portable and give fast results.
Place the device on the clean metal surface.
Press the trigger or button to start the test.
Wait a few seconds for the device to show the results.
Read the screen to see the grade and elements.
Performance Metric | Value/Description |
---|---|
Device Weight | |
Accuracy | Lab-quality in the field |
Carbon Range | 100–300 ppm |
Portability | Easy to carry and use anywhere |
Handheld devices help you test stainless steel for quality control and sorting. You do not need to bring samples to a laboratory.
Laboratory Testing
Some tests need special equipment and trained workers. In a laboratory, you can use OES, AAS, or advanced corrosion tests. For example, the ASTM G48 standard uses ferric chloride to check for pitting corrosion in stainless steel. You must control things like pH, oxygen, and surface finish. Scientists use statistical models to study pit depth and size. These steps help you get exact results when you test stainless steel.
Safety Tips
Always stay safe when you test stainless steel. Wear gloves, goggles, and a lab coat. Work in a well-ventilated area, especially when using acids or grinders. Keep chemicals away from your skin and eyes. Clean up spills right away. Never eat or drink near your testing area.
Note: Safety keeps you healthy and helps you get the best results every time you test stainless steel.
Analyze Stainless Steel Results
Reading Elemental Data
When you check stainless steel, you look at the numbers for each element. Tests show how much chromium, nickel, and molybdenum are in the metal. These numbers tell you what the metal is made of and how it will act. You can use this table to see the usual amount for each element:
Element | Mass Fraction Range (%) |
---|---|
Chromium | |
Cobalt | 0.05 तिर 0.45 |
Copper | 0.06 तिर 3.5 |
Manganese | 0.3 तिर 5.5 |
Molybdenum | 0.02 तिर 3.5 |
Nickel | 0.6 तिर 35 |
Niobium | 0.03 तिर 1.3 |
Phosphorus | 0.01 तिर 0.03 |
Silicon | 0.1 तिर 2 |
Sulfur | 0.02 तिर 0.35 |
Titanium | 0.008 तिर 0.5 |
Vanadium | 0.02 तिर 0.25 |
You can also look at the chart below to compare how much of each element is in stainless steel:
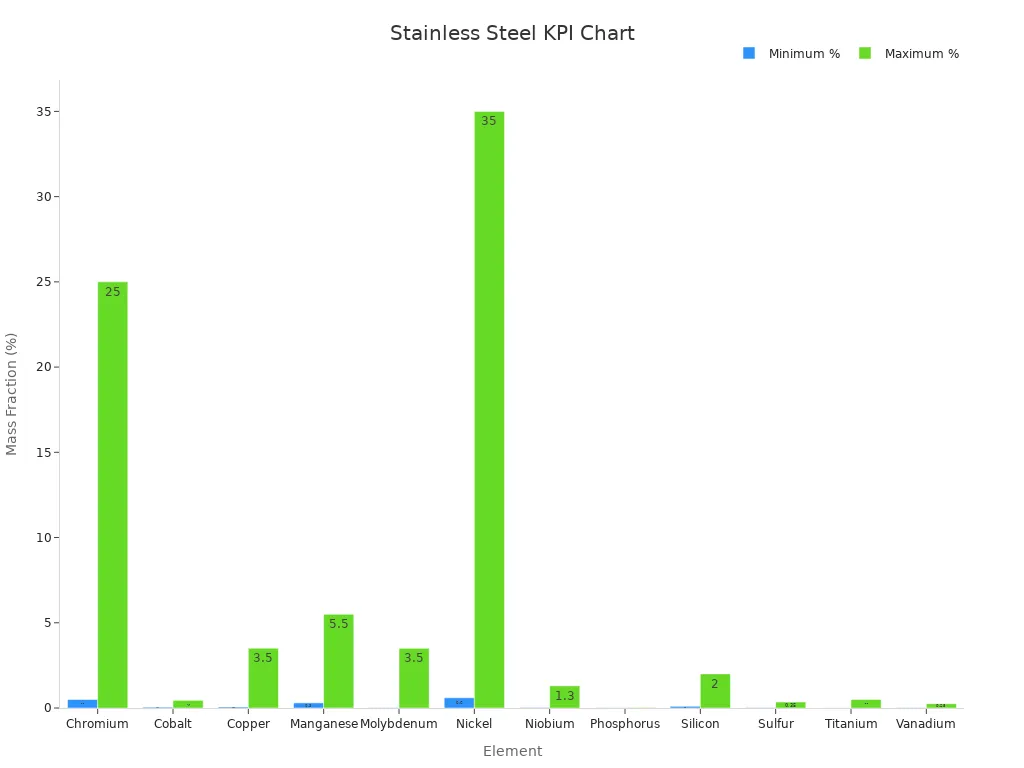
Tip: Always look for the heat number on your sample. This number helps you match your test results to the right batch and check the chemical makeup.
Matching to Grades
You can figure out the stainless steel grade by matching your numbers to known grades. For example, if you see about 18% chromium and 10% nickel, you probably have 304 stainless steel. If molybdenum is over 2%, it could be 316, which fights rust better. Use standard charts to compare your results. This step helps you find out what grade you have and if it meets the rules.
The amounts of carbon, silicon, chromium, manganese, copper, and molybdenum help you pick the grade.
HHXRF and HHLIBS tests can quickly tell grades like 303 and 304 apart.
LIBS can measure very small amounts of carbon, even down to 0.03%, which is important for L and H grades.
If you use test results with corrosion data, you get a full idea of how strong and tough the metal is.
Standards and Specifications
You need to check your results against world standards to make sure your stainless steel is good enough. These rules list what elements and strengths each grade should have. Here are some important ASTM standards:
ASTM Standard | Scope and Elemental Analysis Support |
---|---|
ASTM A269 | Checks seamless and welded austenitic stainless steel tubes for rust resistance and chemical makeup. |
ASTM A213 | Looks at seamless ferritic and austenitic alloy-steel tubes; includes rust and strength tests. |
ASTM A249 | Tests welded austenitic steel tubes; needs chemical and rust checks. |
ASTM A908 | Controls austenitic stainless steel needle tubes; checks chemical and strength rules. |
Note: Following these rules helps you make sure your stainless steel is safe, strong, and resists rust in your projects.
Advanced Stainless Steel Identification Methods
Depth Profiling
Sometimes you need to know how deep a coating goes. Depth profiling helps you see layers under the surface. Neutron Depth Profiling (NDP) can measure light elements in coatings. NDP does not damage your sample. NDP works in a high vacuum. It can find very tiny amounts of elements, even as small as 1E+12 atoms per square centimeter. This method shows how thick a coating is and where each element is. Secondary Ion Mass Spectrometry (SIMS) is another way to check. SIMS can measure elements at the nanometer level. It shows how elements change as you go deeper. These lab tests help you see if a coating is even and meets your needs.
NDP is good for checking thin coatings.
SIMS gives you very detailed depth results.
Both methods help you learn about the layers under the surface.
Surface Analysis
Surface analysis lets you see what is on top of stainless steel. X-ray Photoelectron Spectroscopy (XPS) is often used for this. XPS helps you find out which elements are on the surface. It also shows what chemical states they have. For example, after plasma cleaning, XPS can show changes in carbon, oxygen, iron, and chromium. Water contact angle tests help too. If you treat the surface, the angle gets smaller. This means the surface is easier to wet and bonds better. Other treatments, like microarc oxidation, make the surface rough and full of holes. You can see these changes with special microscopes. These tests help you check if your surface treatment worked.
When to Use Advanced Techniques
Use advanced stainless steel identification when you need more detail than basic tests give. If you want to study coatings, surface treatments, or tricky corrosion, use these methods. Machine learning models can guess how stainless steel will act during cold forming. These models help you pick the right material and save money. Genetic algorithms make tests for special steels more exact. When you need to tell small differences in corrosion or surface changes, advanced methods work better. You can use scores like accuracy and precision to see if you need these tests. Advanced techniques help you solve hard problems that simple tests cannot fix.
Method Comparison Table

Summary Table
You can use this table to compare the main stainless steel analysis methods. It shows how each method works, where you can use it, and what it is best for. This helps you pick the right test for your needs.
Method | Speed | Accuracy | Field Use | Lab Use | Elements Detected | Best For |
---|---|---|---|---|---|---|
Seconds | High | Yes | Yes | Most metals (not C) | Fast sorting, grade ID | |
OES | Minutes | Very High | छैन | Yes | Most metals (inc. C) | Full grade check, trace elements |
ICP-OES | Minutes | Very High | छैन | Yes | Over 30 elements | Impurity check, lab analysis |
AAS | Minutes | High | छैन | Yes | Select elements | Nickel, chromium, trace metals |
XPS | Hours | Very High | छैन | Yes | Surface elements | Coatings, surface treatments |
Magnet Test | Seconds | Moderate | Yes | Yes | Magnetic response | Quick family check |
Visual Test | Seconds | Moderate | Yes | Yes | Surface features | First look, finish check |
Spot/Spark Test | Seconds | Moderate | Yes | Yes | Key elements | Fast sorting, basic ID |
Tip: Use this table when you want to compare speed, accuracy, and where you can use each test.
Choosing the Right Method
You need to choose the best test for your job. Think about what you want to find out and where you will work. If you need to know the exact elements in your steel, use a chemical analysis like XRF or OES. These tests help you pick the right grade for corrosion resistance and strength. If you want to check how strong your steel is, use tensile or hardness testing. These tests show if your steel can handle heavy loads or wear.
Use ASTM standards to make sure your test results are reliable.
Look at lab reports for numbers like yield strength and hardness. These numbers help you decide if your steel is safe to use.
Machine learning models can help you predict how your steel will react in different environments. These models use data from your test to guess corrosion behavior. You can save time and money by using these tools instead of running many tests.
If you need to check a coating or surface treatment, pick XPS or depth profiling. These tests show what is on the surface and how deep it goes.
Remember: Good testing helps you avoid product failure and keeps your projects safe.
You have many ways to test stainless steel. XRF and OES give you fast and accurate results for most grades. Use XPS or SEM when you need to check surface changes or corrosion. Always match your method to your job. Testing helps you spot corrosion early and keep your projects safe.
Clean samples and follow safety steps every time.
Record results to track corrosion and material changes.
Good testing and careful records help you prevent corrosion and improve your work.
FAQ
How can you tell if stainless steel is 304 or 316?
You can use a chemical spot test to check for molybdenum. Grade 316 has molybdenum, but 304 does not. XRF analyzers also help you see the difference by showing the element amounts.
Is a magnet test enough to identify stainless steel grade?
A magnet test helps you sort stainless steel into families. It does not give you the exact grade. Always use another method, like XRF or a chemical test, for full identification.
What is the fastest way to check stainless steel grade in the field?
Handheld XRF analyzers give you results in seconds. You just place the device on the metal and press the button. You see the grade and element amounts right away.
Can you test stainless steel without damaging it?
Yes, you can use XRF or magnet tests. These methods do not harm the metal. Chemical spot tests may leave small marks, but they do not change the metal’s strength.
Why do you need to match test results to standards?
Matching your results to standards, like ASTM, helps you make sure your stainless steel is safe and meets project rules. This step protects your work and keeps quality high.
Whatsapp
QR कोड स्क्यान गर्नुहोस् हामी संग व्हाट्सएप च्याट सुरु गर्न.