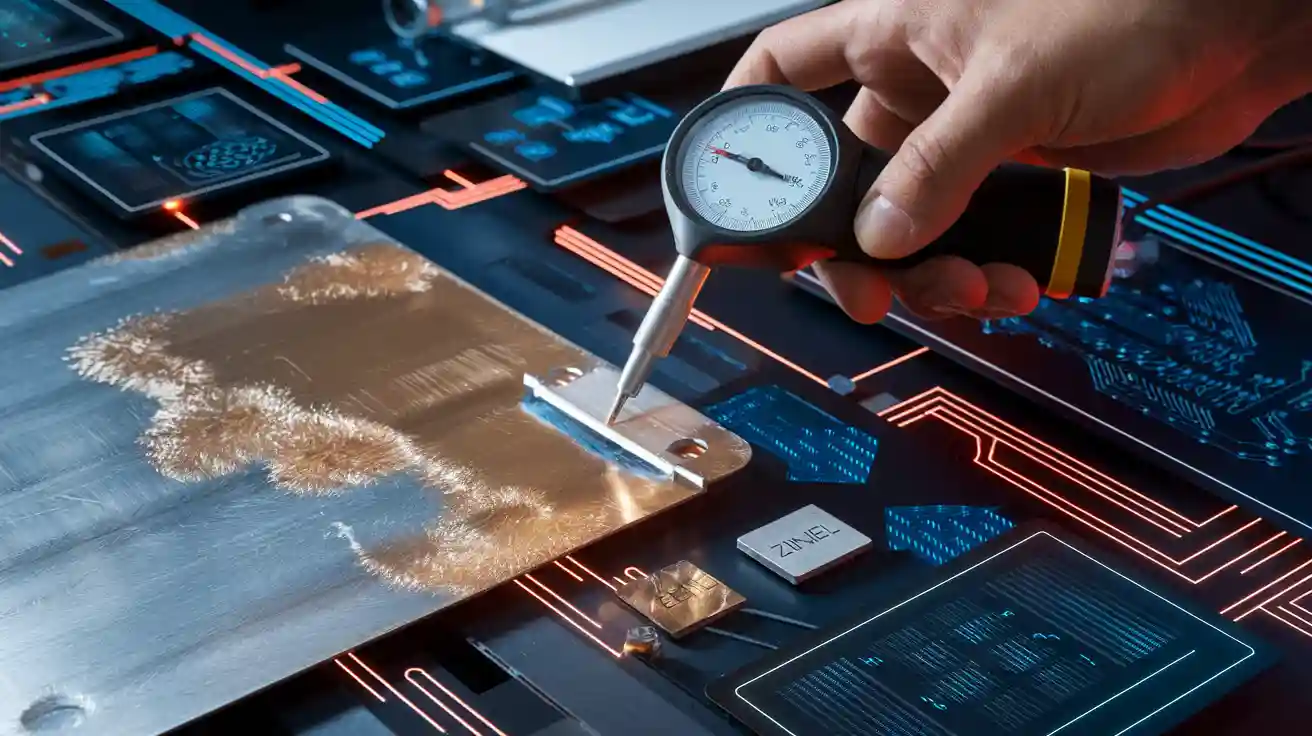
Accurate coating thickness measurement is crucial in factories, especially when it comes to about zinc and nickel coating thickness analysis. Real-time monitoring systems ensure the thickness of zinc and nickel coatings stays within the correct range, reducing waste and maintaining consistent product quality. The industry relies on advanced techniques such as X-ray fluorescence and eddy current gauges for about zinc and nickel coating thickness analysis, ensuring reliable results. Using approved measurement methods and adhering to international standards helps prevent costly errors. Incorrect coating thickness can lead to product failures or increased expenses. By following best practices for about zinc and nickel coating thickness analysis, companies can avoid these issues and maintain compliance with industry regulations.
Takeaways utama
Measuring zinc and nickel coating thickness helps stop rust. It makes products last longer. This also stops expensive repairs or things breaking.
Pendarfluor sinar-X (Xrf) and magnetic or eddy current gauges are the best ways to measure thickness. These methods are very accurate and used a lot.
Following industry standards like ASTM and ISO makes sure coatings are good. It keeps products safe and follows the rules.
Good surface preparation is important. Tools must be checked often. Skilled workers are needed for correct thickness measurements.
Keeping good records and training workers helps keep quality high. It also helps follow rules and stops costly mistakes.
About Zinc and Nickel Coating Thickness Analysis
Why Coating Thickness Matters
Manufacturers use about zinc and nickel coating thickness analysis to check product quality. The right coating thickness keeps metal safe from rust and damage. If the coating is too thin, metal can rust, crack, or peel early. If the coating is too thick, it might crack or not stick well. This can cost a lot to fix or replace. Doing about zinc and nickel coating thickness analysis the right way helps products last longer. It also keeps them strong. For example, in the pharmaceutical industry, coatings must be thick enough to protect. Even small changes in thickness can change how well they work. In cars, planes, and electronics, measuring coating thickness is very important for safety.
Nota: Automated systems and AI now help make about zinc and nickel coating thickness analysis more exact. This helps companies make better products that last longer.
Typical Thickness Ranges
About zinc and nickel coating thickness analysis is used in many ways. The table below shows common thickness ranges and where they are used:
Coating Class | Zinc Coating Thickness Range | Typical Application Sector | Measurement Techniques |
---|---|---|---|
Class 1 | > 80 μm (hot-dip galvanised) | Steel construction | Magnetic induction, Eddy current |
Class 2 | Up to ~10 μm (galvanic/dip) | Automotive body | Phase-sensitive eddy current, Magnetic induction |
Class 3 | Up to ~30 μm | Automotive piping | Phase-sensitive eddy current, Magnetic induction |
Class 4 | Zinc-nickel alloy layer | High corrosion risk parts | Magnetic induction, Eddy current |
Electroplated zinc-nickel coatings are usually 8 ke 14 μm thick. These coatings protect against rust and wear. They are important for car fasteners, airplane parts, and electronics. The need for zinc-nickel coatings is growing. North America uses the most because of high demand.
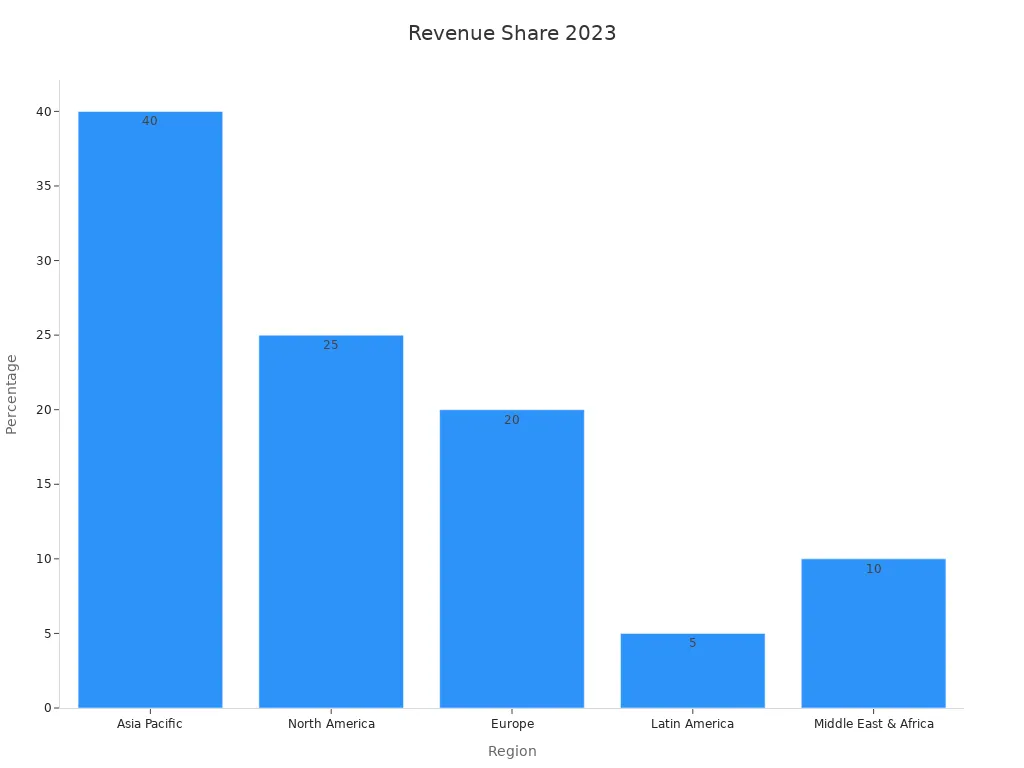
It is important to measure about zinc and nickel coating thickness correctly. Hand-held tools and machines help make sure coatings are the right thickness for each job.
Coating Thickness Standards
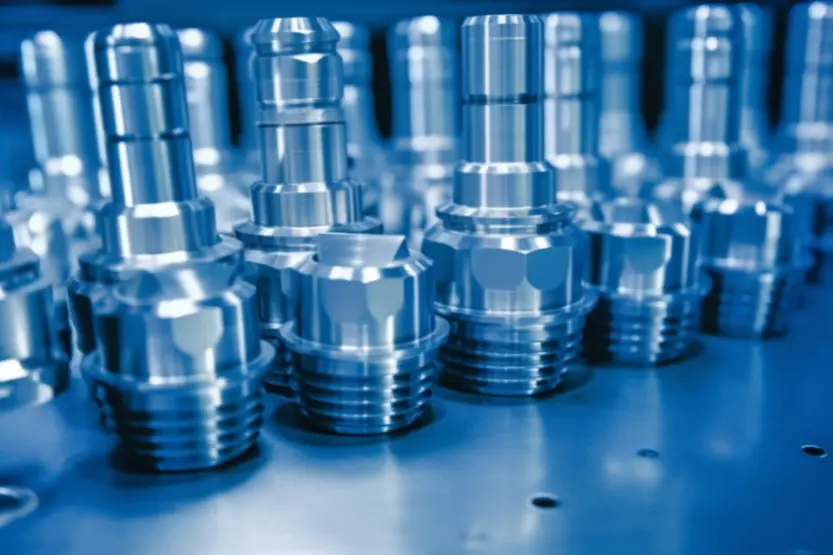
Zinc Coating Standards
The industry uses clear rules to control zinc coating thickness and quality. ASTM B633 is the main rule for zinc coatings on iron and steel. This rule tells how thick the coating should be. It also says how it should look and how well it should stop rust. ASTM B633 helps companies make strong products. It makes sure zinc coatings protect metal from rust and damage.
ASTM F1941/F1941M-16(2025) helps with zinc coatings for fasteners. This rule explains how to put on coatings and how thick they should be. It also helps stop problems like hydrogen embrittlement. These rules help companies keep products safe and high quality.
Nota: ASTM D1186 and ASTM D1400 tell how to measure coating thickness. They use magnetic tools and micrometers. These tools help check if coatings are thick enough.
Nickel and Zinc-Nickel Standards
Nickel and zinc-nickel coatings also have strict rules. ASTM B841 tells what zinc-nickel alloy coatings need. This rule says how thick the coating should be. It also tells how it should look and how well it stops rust. ASTM B841 helps nickel and zinc-nickel coatings last longer. It keeps metal safe in tough places.
ASTM B571 checks how well nickel and zinc-nickel coatings stick to metal. Good sticking keeps the coating from peeling or cracking. ASTM B117 is a salt spray test. It checks how well the coating stops rust. These tests help make sure nickel and zinc-nickel coatings are good quality.
The table below shows important things from coating rules:
Requirement | Standard(s) | Purpose |
---|---|---|
ASTM D1186, ASTM D1400 | Makes sure coatings are thick enough | |
Adhesion | ASTM D3359, ASTM B571 | Checks if coatings stick well |
Corrosion Resistance | ASTM B117, ASTM D1654 | Tests if coatings stop rust and damage |
Companies must follow these rules to keep products safe. Meeting thickness, sticking, and rust tests helps avoid big problems. It also helps people trust the products.
Measuring Coating Thickness: Methods
Measuring coating thickness the right way keeps products good. It also helps companies follow the rules. There are many ways to check coating thickness. Each way has good and bad points. The best method depends on the coating, the base material, and how exact you need to be. The next parts talk about the most used ways to measure coating thickness.
Pendarfluor sinar-X (Xrf)
XRF is a very exact and popular way to check coating thickness. It does not hurt the coating. XRF uses X-rays to make atoms in the coating give off special X-rays. The tool sees these X-rays and figures out how thick the coating is. XRF is very accurate and does not make many mistakes. It works for one layer or many layers.
New XRF tools have special tubes, auto-focus, and distance checks. These things help keep the sample at the best spot. They also make the results better. People can use XRF on many coatings and base materials. It works for simple zinc and for zinc-nickel alloys. XRF can also take pictures. This helps workers see details and check quality in cars, planes, and electronics.
Petua: XRF tools give steady, repeatable, and safe checks. They are great for regular quality tests and meeting rules.
Feature | Penerangan |
---|---|
Detector Type | Proportional counter tube for accurate measurement |
Auto-Focus Function | Maintains optimal distance for high precision |
Distance Correction | Ensures measurement accuracy |
Application Versatility | Suitable for single-layer, multi-layer, and alloy coatings |
Imaging Capability | Combines wide view and narrow field imaging for detailed analysis |
Magnetic and Eddy Current Gauges
Magnetic and eddy current gauges are important ways to check coating thickness. They do not damage the coating. Magnetic gauges look at changes in magnetic force near a metal base. Eddy current gauges use fast currents in non-magnetic bases and check changes in electricity. Both ways are usually right within about 1%. They work well for zinc and nickel coatings.
These gauges have probes that press the same each time. This helps different people get the same results. The screen shows the answer right away. Workers check the tools with known standards to make sure they are right. This works even if the base, roughness, or shape changes. Magnetic gauges follow ASTM D1186 and ISO 2178 rules. Eddy current gauges follow ASTM B244 and ISO 2360. Car, boat, and plane makers use these ways for quick, repeatable, and safe tests.
Beta Backscatter
Beta backscatter uses beta rays to check coating thickness. The tool sends beta particles to the coated part. The number of particles that bounce back shows how thick and dense the coating is. This way works for coatings on metal and non-metal bases.
Beta backscatter does not hurt the coating and is good for thin coatings. Other ways may not work as well for thin layers. But, workers must be careful because it uses radioactive parts. They must follow safety rules to keep everyone safe and get good results.
Mechanical Cross-Sectioning
Mechanical cross-sectioning is a direct and detailed way to check coating thickness. Workers cut a small piece of the coated part. They put it in resin and polish it. Then, they use a microscope to measure the thickness and look at the inside.
This way shows if the coating is even, has holes, or sticks well. For example, special microscope pictures show holes and how the coating is made. Workers can see layers, holes, and different parts. This proves the coating is good and the right thickness. Mechanical cross-sectioning is the best way to check other methods. But it breaks the sample and takes a long time.
Comparative Accuracy of Measurement Methods
The table below shows how well different ways measure coating thickness and what problems they might have:
Measurement Method | Accuracy / Uncertainty | Sensitivity / Limitations | Notes / Remarks |
---|---|---|---|
Pneumatically Actuated Length Gauges | Overestimates thickness | Sensitive to surface roughness | |
Optical Confocal Distance Sensors | Close to reference thickness | Sensitive to disturbances | Limited precision for layer-by-layer control |
Optical Distance Measurement | High precision (~2 µm) | Independent of surface roughness and thermal expansion | Uncertainty increases with number of layers |
Eddy Current Methods | Not detailed | N/A | Alternative method without detailed accuracy data |
Capacitance-Based Sensors | Not detailed | N/A | Alternative method without detailed accuracy data |
Laser-Ultrasonics | Not detailed | N/A | Alternative method without detailed accuracy data |
Thermography | Not detailed | N/A | Alternative method without detailed accuracy data |
Terahertz Techniques | Not detailed | N/A | Alternative method without detailed accuracy data |
Nota: XRF and magnetic or eddy current gauges are the top choices for checking coating thickness. They are exact, give the same results each time, and meet industry rules.
Method Selection
Suitability for Zinc and Nickel
Picking the best way to measure coating thickness depends on a few things. You need to think about the type of coating, what it is on, and how exact you need to be. For zinc and nickel coatings, experts often use more than one method. This helps them get results they can trust. X-ray fluorescence and magnetic gauges are used a lot. They give correct and steady readings for both one-layer and many-layer coatings. Other ways, like adhesion tests and checking how fast something rusts, also help see if the coating is strong and good.
When picking a way to measure, you have to think about some things:
If the sample is rough or not smooth, it can change the results.
How well the tool can see small changes matters.
How you set up the tool and the weather, like heat or wetness, can change what you find.
Following the rules for the industry makes sure the way you pick is good.
Some tools use more than one way to measure. For example, they might use both magnetic induction and eddy current. This helps them work on different shapes and materials. Tools that send data right away and use special computer programs help keep track of quality and save the results.
Pros and Cons
Every way to measure coating thickness has good and bad points. The table below shows some of the most used ways for zinc and nickel coatings:
Kaedah | Advantages | Disadvantages | Suitable Conditions |
---|---|---|---|
Magnetic Thickness Method | Very correct, simple to use, not expensive | Only works for non-magnetic coatings on magnetic bases | Keluli, iron, silver, nickel bases |
Eddy Current Method | Sees small details, good for layers that do not carry electricity | Not as correct as magnetic, needs a gap in conductivity | Paint, plastic, anodic oxide on metals that carry electricity |
Does not hurt the coating, very exact, works for many layers | Costs more, needs to be set up right | Many kinds of coatings and materials | |
Mechanical Cross-Sectioning | Lets you look right at the coating, gives lots of details | Breaks the sample, takes a long time | Used in labs, checks quality |
Petua: In most factories, using ways that do not hurt the coating along with lab tests helps make sure measuring is fast and correct.
Factors Affecting Accuracy
Substrate and Surface
The kind of metal and the surface condition are very important for coating thickness accuracy. Different metals and alloys act differently when coated. If the surface is rough or dirty, the coating may not spread evenly. Clean and smooth surfaces help the coating stick better. If the surface is bumpy, the coating can pile up in some spots and be thin in others. Odd shapes make it hard to put the coating on evenly. Weather, like heat and wetness, can change how the coating dries or sticks.
Cleaning the surface gets rid of oil, dust, and dirt.
Making the surface rough, like with sandblasting, helps the coating hold on.
What the metal is made of changes how the coating bonds and how well measuring works.
High wetness can cause water drops, and low wetness can make static and dust, both can change coating thickness.
Nota: Rules like ISO 2360 and ASTM D7091 explain how to measure coating thickness on different metals.
Calibration and Standards
Getting the right measurement means using good calibration standards. Factories often make their own electroplated standards. These cost less than special reference materials but still work well. Workers check these standards with a microscope to see if the thickness is right. Using these standards helps make measurements more exact, especially with Xrf.
Calibration standards should be like the sample’s coating and metal for best results.
Even thickness in the standard helps keep measurements steady.
Tests show that homemade standards can keep thickness changes under 5%, which is good for the industry.
Methods without standards can have bigger mistakes, especially with many layers.
Petua: Checking calibration often and using the right standards for each coating and metal helps keep measurements steady and correct.
Operator Skill
How well a worker does the job also changes coating thickness accuracy. Workers need to know how to use each method and follow the right steps. If they do things differently each time, mistakes can happen. Training helps workers learn how to get surfaces ready, use tools, and read results. Taking more than one reading and following good steps helps stop errors.
Skilled workers pick the best way to measure for each job.
They check their tools before using them and follow the rules.
They know how weather and other changes can affect what they find.
A trained team makes sure coating thickness checks are right and follow the rules.
Best Practices
Calibration and Quality Assurance
Quality checks for coating thickness start with calibrated XRF tools and reference standards. These tools help workers get correct and repeatable results. Studies show that using special math for calibration makes results better. The error can be as low as 0.4% for iron and 1% for zinc. Regular care by trained workers keeps XRF tools working well and helps them last longer.
People in this field follow careful steps to make sure measurements are good:
Take at least five spot checks on each sample. Pick spots that show the whole surface.
Use gauges that are checked and meet maker and ASTM D7091 rules.
Calibrate tools before each work shift, after heavy use, or if dropped.
Make sure the gauge is right for the range you need.
Keep records of calibration and follow yearly check-up plans.
Check the gauge during use to make sure it stays correct.
Only let trained people do calibration and checks.
Petua: Workers should keep learning and get certificates. This helps keep quality high and lowers mistakes.
Compliance and Documentation
Good records help with quality and following rules in the industry. Companies in telecom, electronics, and aerospace keep detailed records to meet ASTM, ISO, OSHA, FDA, and CSA rules. Baru pengujis often link to software and cloud systems, making it easier to manage data.
Important steps for following rules and keeping records include:
Look at old coating reports and care records before checking.
Get tools ready, like DFT gauges and adhesion testers.
Write down all measurements, notes, and photos using rating systems.
Make full reports with summaries, findings, and rule checks for asset teams.
Always mention international rules like ISO 12944 and ASTM in reports.
Nota: Keeping good records and following check steps helps protect assets and meet industry rules.
Following the rules in the industry helps people measure coating thickness the right way. Using tools that are checked and picking the best way to measure makes results better. Experts can make their work more trustworthy by:
Making sure the surface is ready before coating, instead of doing extra things like feathering. Studies say feathering does not help the coating last longer and just adds more work.
Always checking that tools are set right and keeping records up to date.
Going to training often so they know the newest rules.
Learning new things all the time and following the latest rules helps people get good results and avoid expensive mistakes.
Soalan Lazim
What is the most accurate method for measuring zinc or nickel coating thickness?
Pendarfluor sinar-X (Xrf) is the best way to measure most coatings. Many companies use XRF because it gives exact and steady results. XRF does not harm the sample when checking thickness.
How often should calibration of measurement instruments occur?
Experts say to calibrate tools before each work shift. You should also calibrate after using the tool a lot or if you drop it. Doing this often helps make sure measurements are always right.
Which standards apply to zinc-nickel coating thickness?
ASTM B841 is the rule for zinc-nickel coatings. ASTM B117 and ASTM B571 are for checking rust protection and how well the coating sticks. Using these rules helps companies follow industry needs.
Can operators use the same method for all substrates?
Tidak, not every way works for every kind of metal. Magnetic gauges are good for metals that stick to magnets. Eddy current gauges work best on metals that do not stick to magnets. Workers must pick the right tool for each job.
Why does surface preparation matter in coating thickness analysis?
Getting the surface ready takes away dirt, oil, and rust. A clean and smooth surface helps the coating stick better. This also makes thickness checks more correct.
WhatsApp
Imbas kod QR untuk memulakan sembang WhatsApp dengan kami.